Table of Contents
Rapid Tooling Services
Prototype and Short-Run Injection Moldings
Exact plastic material as final design
Molding quantity started from 100 pieces
Much lower cost than production mold
Fast delivery in Days
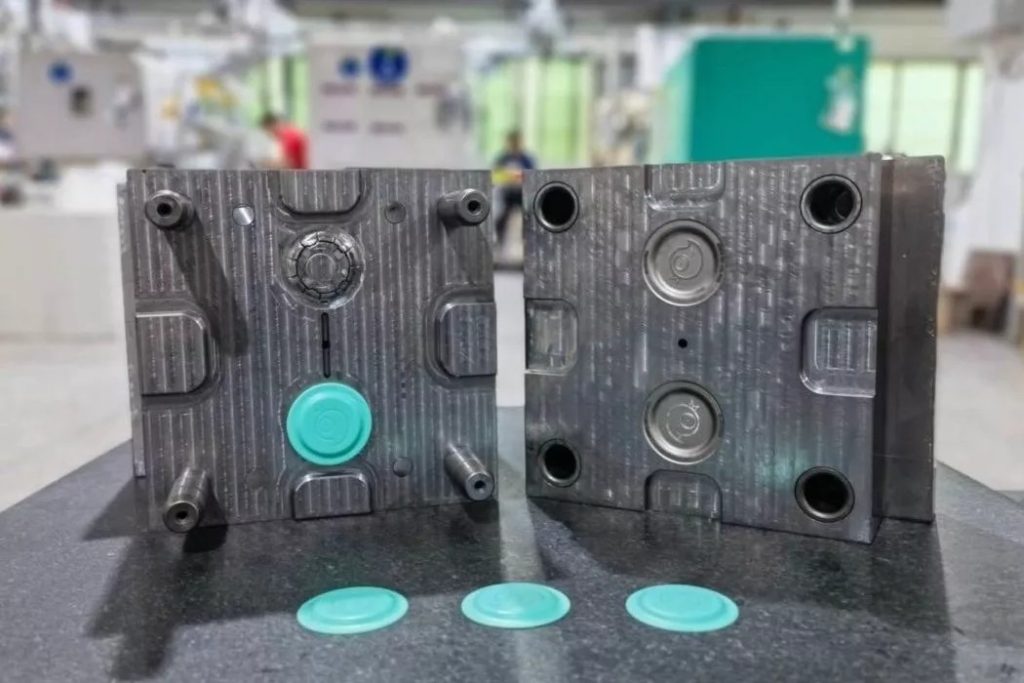
XinYang leverages its expertise, engineering prowess, and cutting-edge technology to deliver top-notch rapid tooling solutions for prototypes and small-scale production runs. Our dedicated team collaborates closely with every client to guarantee the development of an impeccable solution. Our track record speaks volumes about our proficiency. At XinYang, our team is fully equipped to cater to your rapid tooling and mass production mold making needs. If you are prepared to commence mass production, explore our injection molding services for further information.
Rapid Tooling Processes
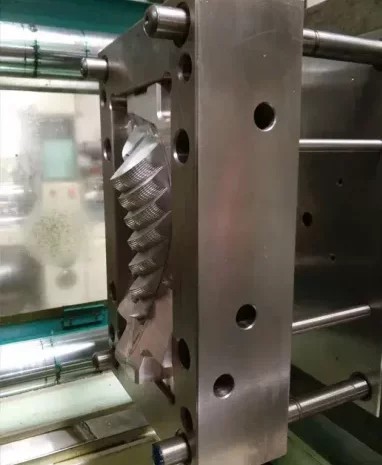
Fast Mold Making
Utilizing machined aluminum or soft steel mold cavities is essential for achieving quick injection mold production for low-volume manufacturing. Streamlining the mold design and incorporating standard mold components and bases can further expedite the process.
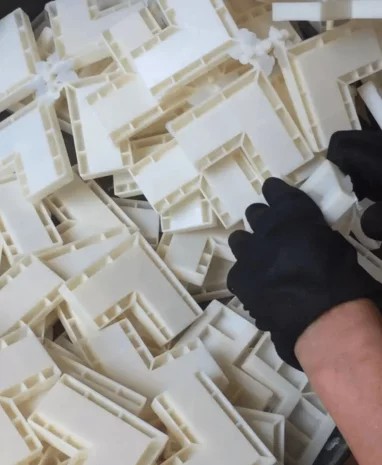
Rapid Injection Molding
In addition to our standard production molding services, we have more than 10 injection molding machines available for prototype or small batch molding. The molds will be promptly loaded onto the machines without any delays.
What is Rapid Tooling
Rapid tooling, also referred to as prototype tooling or bridge tooling, offers a quick and cost-effective method for producing low-volume injection molded plastic parts. After the aluminum or steel mold is produced using rapid tooling, it can be integrated into the molding process to manufacture numerous replicas of a part. This technique is commonly employed to generate moldings for rapid prototyping requirements within a condensed timeline, or to serve as an interim solution prior to high-volume manufacturing.
The rapid tooling procedure consists of fabricating a mold from aluminum or soft steel, utilizing a pre-made mold base, and manually inserting the necessary components. Rapid tooling stands out as a top-notch approach for meeting the requirements of small batch orders intended for marketing samples, product assessments, and process development.
Conventional tooling can be too costly for small-scale projects. Our tailored rapid tooling service offers a budget-friendly option for low-volume needs, especially when mass production is not required. The rapid production tooling method is frequently utilized in industrial environments for prototyping and troubleshooting design problems, making mold making more accessible.
At XinYang, our usual approach involves producing quick molds through CNC machining and EDM, with occasional utilization of additive techniques like 3D printing technologies.
Rapid Tooling Materials

Aluminum Mold Tooling
Aluminum mold tooling is an excellent option for prototyping, offering a cost-effective solution for manufacturing molded parts. Due to their ease of cutting, aluminum molds can lower tooling expenses by 15–25% in comparison to alternative mold materials, while also decreasing cycle times by as much as 40%. This results in quicker production for our clients.
Aluminum’s ability to evenly dissipate heat results in enhanced dimensional stability in tooling, leading to a notable decrease in deformation and waste generation throughout the production process. It is crucial to highlight that while aluminum falls short in strength compared to steel, it boasts a shorter lifespan and is less suitable for high-volume manufacturing operations.
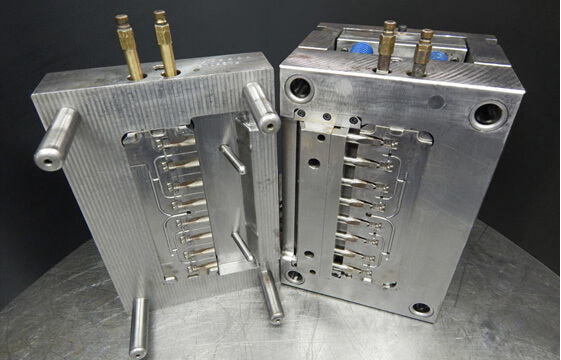
Steel Mold Tooling
Steel is a durable and reliable material for tooling, but it may not be the best choice for every situation. Unlike aluminum, steel molds have a longer lifespan, making them perfect for mass production. Additionally, steel is capable of creating molds from tough engineering plastics that can withstand wear and tear as well as corrosion.
Despite its numerous advantages, steel is a pricier option for tooling material compared to aluminum, and it also demands a longer production time for molds and prototypes.
Prototype Injection Molding Materials
In general, plastics suitable for injection molding can also be molded using prototype molds. The following are the most frequently molded plastics. For materials not listed, kindly reach out to our team for further details.
Thermoplastics
- ABS
- Acetal Copolymer
- HDPE
- LLDPE
- PC/PBT
- PET
- Polycarbonate
- PPE/PS
- TPU
.
- ABS/PC
- Acetal Homopolymer/Delrin
- LCP
- Nylon
- PEEK
- PETG
- Polypropylene
- PS
.
- Acetal
- ETPU
- LDPE
- PBT
- PEI
- PMMA (Acrylic, Plexiglas)
- PPA
- PSU
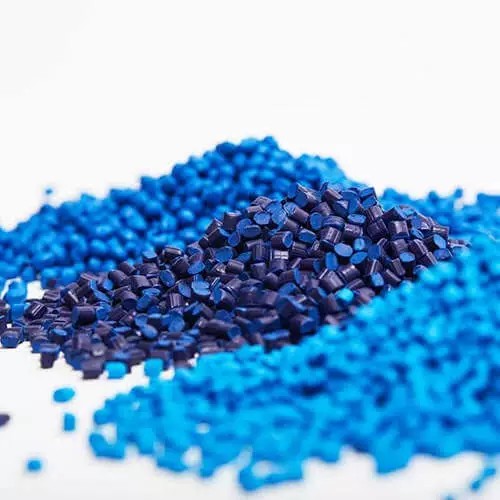
Thermosets
- Standard silicone (30, 40, 50, 60, and 70 durometers)
- Optical-grade silicone
- Medical-grade silicone
- Fluorosilicone (fuel and oil resistant)
Rapid Tooling & Mold Making Projects
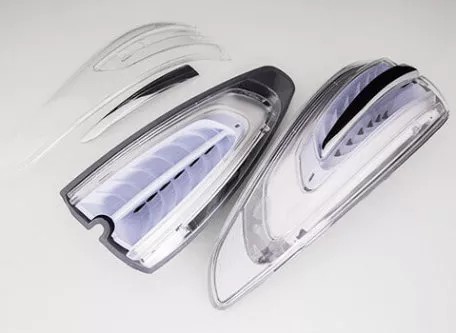
Could you envision the challenge of creating prototype tools for more than 30 components within a mere two-month timeframe? Our client was in urgent need of 200-300 sets of tail lights for testing purposes, yet the mass production tools would not have been available for another eight months. Consequently, they required a cost-effective solution to obtain high-quality moldings by their deadline, without relying on production tools.
To complete this tail light project, we were required to manufacture various components such as a housing, reflector, light guide, bezel, outer lens, and other parts within a limited timeframe. The overall size of the assembly was approximately 600 x 400 x 150 mm, making it relatively large. Additionally, the customer expressed the need to test the materials used in the prototype. Given these requirements, 3D printing, CNC machining, and vacuum casting were deemed unsuitable, leaving prototype molding as the sole viable option. You can click here to view this particular case.