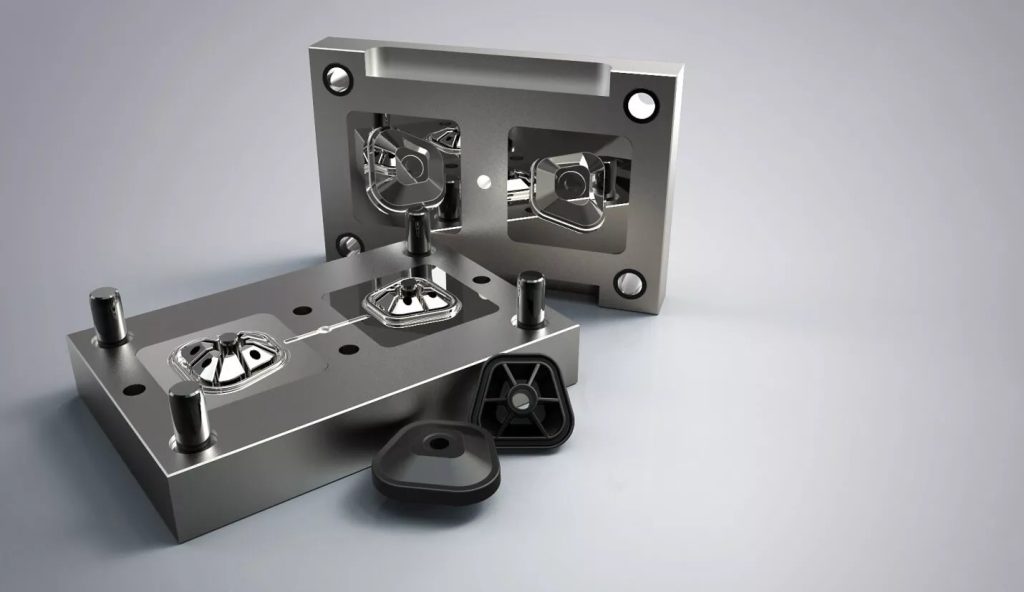
Rapid injection molding method is revolutionizing how products come to life, blending efficiency and speed with engineering. This process makes it possible to manufacture many durable consumer and industrial items cheaper than everything else. It produces around 32% of plastics by weight.
Inhoudsopgave
What is Rapid Injection Molding?
Rapid injection molding is a type of injection molding designed to produce parts quickly and efficiently, bridging the gap between initial prototypes and mass production. It is exceptionally suited for generating anywhere from a few units to 10,000 parts within a matter of weeks. It embodies the intersection of speed and accuracy, making it a go-to choice for companies across various industries.
They are capable enough to manufacture anywhere from a few parts to thousands. There are many manufacturers who use this process for producing molding parts as per their client’s requirements. Most essentially, this is the most convenient way to meet the client’s needs and specifications effectively sans hassle.
How is Rapid Injection Molding different from Standard Injection Molding?
While both processes share the core principle of injecting molten material into a mold, rapid injection molding is distinguished by its speed and flexibility. Standard injection molding is typically geared towards high-volume production, necessitating more extensive tooling and setup time. In contrast, rapid injection molding focuses on accelerating the production process, making it ideal for short runs and tight deadlines.
How Does Rapid Injection Molding Work?
At its core, rapid injection molding involves injecting thermoplastic resins into a mold at high pressure, which then cools and solidifies to form the desired part. This technique is renowned for its speed, which does not compromise the quality or the versatility of the produced parts. Whether for prototyping or small to medium-sized production runs, this method stands out for its ability to deliver reliable results swiftly.
What are The Stages of Rapid Injection Molding
To demystify the process, it’s crucial to break down the main stages involved in rapid injection molding. Each phase plays its role in ensuring the final product meets the specified requirements with precision:
- Design and Prototyping: Initially, a detailed design of the part is created using CAD software. This stage is critical for identifying and incorporating essential design features such as wall thickness, surface finish, and material selection. Rapid prototyping techniques like 3D printing may be used to create a physical prototype for evaluation and testing.
- Mold Making: Once the design is finalized, the production of the mold begins. Aluminum molds are commonly used due to their cost-effectiveness and shorter lead times compared to traditional steel molds. CNC machining and electrical discharge machining (EDM) are techniques employed to craft these molds with high accuracy.
- Material Selection: Selecting the appropriate resin material is crucial for the project. Factors like the part’s end use, mechanical properties, and aesthetic requirements guide this selection process. Engineering resins, ABS, polypropylene, and polycarbonate are among the polymers often chosen for their durability and performance.
- Injection Molding Process: The selected material is melted and injected into the mold cavity under high pressure using an injection molding machine. This phase is meticulously monitored to ensure optimal molding conditions and to achieve the desired quality.
- Cooling and Ejection: After injection, the part cools and solidifies within the mold. Cooling channels within the mold help in managing the cooling rate for even solidification. Once cooled, the part is ejected from the mold, marking the completion of the molding cycle.
- Post-Processing: Depending on the part design and application, post-processing steps such as drilling, painting, or assembly might be necessary. These additional processes are carried out to refine the part’s appearance, enhance its properties, or prepare it for its final application.
- Quality Assurance: Each part undergoes a thorough inspection to ensure it meets the required specifications and quality standards. Measurements and tests are conducted to assess the part’s dimensions, material properties, and overall integrity.
- Iteration if Necessary: Rapid injection molding allows for quick iterations based on feedback or testing results. Design modifications can be efficiently implemented, demonstrating the process’s flexibility in adapting to specific needs.
What is the Equipment Used for Rapid Injection Molding?
Central to rapid injection molding is a range of specialized equipment, each serving a critical role in the creation of high-quality parts, tooling and prototypes.
The equipment used in rapid injection molding is designed to optimize production speed and part quality.
Here’s a rundown of the main equipment involved:
- Injection Molding Machines: These are the heart of the process, where the actual molding takes place. An injection molding machine melts the plastic material and inject it into molds under high pressure.
- CNC Machining Centers: Utilized for creating the molds into which the plastic is injected. CNC machining provides the precision necessary to manufacture molds that meet specific part tolerances and geometries.
- Electrical Discharge Machining (EDM) Equipment: This is used for creating more complex molds with intricate details. EDM allows for the shaping of molds by using electrical discharges (sparks).
- 3D Printing Devices: Often used in the prototyping stage, 3D printers can produce mold prototypes or parts directly from CAD data, significantly speeding up the design verification process.
- Aluminum and Steel for Molds: Material selection for molds is crucial, with aluminum being a popular choice for its quick turnaround times and cost-effectiveness in rapid prototyping.
- Plastic Resin Dryers: Before injection, plastic resins need to be dried to prevent any quality issues in the final product. Resin dryers are essential to prepare the material for molding.
- Temperature Controllers and Chillers: These regulate the temperature of the mold and the plastic material, ensuring optimal conditions for high-quality part production.
- Part Removal Robots and Automation Equipment: In some setups, robots and automation tools are used to enhance efficiency and consistency by removing the finished parts from the machine and performing secondary operations.
How Are Molds Used for Rapid Injection Molding Different Than Standard Injection Molds?
Molds for rapid injection molding differ significantly from those used in traditional injection molding, mainly due to the focus on speed and flexibility.
- Material: Rapid injection molds are often made from aluminum or other materials that are easier and faster to machine than the traditional tool steels used in standard molds. This material choice significantly reduces lead times for mold production.
- Design Simplicity: Molds designed for rapid injection molding are typically simpler, focusing on essential features that allow for quicker production. They may have fewer cavities and simpler mechanisms, which speeds up the manufacturing process.
- Lifespan and Volume: Molds for rapid injection molding are intended for shorter production runs than standard molds. While a standard mold might be designed to produce millions of parts, a rapid injection mold may be targeted for thousands to tens of thousands of parts, aligning with the goals of prototyping or low-volume production.
- Cost: Due to their simpler design and material selection, molds for rapid injection molding are generally less expensive to produce than their standard counterparts. This cost-effectiveness enables companies to experiment with different designs without a significant financial burden.
What are the Benefits of Rapid Injection Molding?
Rapid injection molding stands out for its ability to streamline the journey from conceptual design to finished product, offering plenty of advantages.
Speed and Efficiency in Prototyping and Production
One of the most significant advantages of rapid injection molding is its unmatched speed and efficiency. The process allows for the swift development of prototypes, facilitating a faster transition to production stages. This rapid progression is crucial for beating competitors to market and testing concepts without costly delays.
Cost-effectiveness for Low to Medium Volume Production
Rapid injection molding is cost-effective, especially for low to medium volume productions. The use of aluminum molds, which are less expensive and quicker to manufacture than traditional steel molds, significantly reduces upfront costs. This affordability enables companies to manage their budget more effectively while still achieving high-quality outputs.
Versatility in Material and Design Capabilities
The process offers remarkable versatility, accommodating a wide range of materials and design specifications. Whether you’re working with engineering resins, ABS, polypropylene, or polycarbonate, rapid injection molding meets diverse material requirements. Additionally, it supports complex designs, ensuring that the final parts meet precise specifications.
Improved Precision and Consistency in Part Production
Achieving precision and consistency is paramount in manufacturing. Rapid injection molding excels in producing parts with tight tolerances and uniform quality. This precision ensures that every part functions correctly, meeting or exceeding the performance standards set by the project.
Enhanced Product Development Flexibility
Rapid injection molding provides unparalleled flexibility in product development. Design changes can be quickly implemented without significant cost penalties, allowing for iterative design improvements. This adaptability is essential for optimizing product design and functionality.
Reduction in Time to Market
A direct consequence of the process’s speed and efficiency is a substantial reduction in time to market. Companies can swiftly move from concept to commercialization, gaining a competitive edge in fast-paced markets. This agility is crucial for responding to consumer demands and market trends.
Sustainable Manufacturing and Reduced Waste
The precision of rapid injection molding leads to minimal waste production, aligning with sustainable manufacturing practices. The efficient use of materials not only conserves resources but also reduces the overall environmental footprint of the manufacturing process.
Ability to Quickly Respond to Market Changes
Lastly, rapid injection molding allows companies to respond swiftly to market changes. Whether adjusting to new consumer preferences or incorporating the latest technological advancements, this process supports dynamic adaptation, ensuring businesses remain relevant and competitive.
What are Applications and Industries Benefiting from Rapid Injection Molding?
Utilizing rapid injection molding has become more and more prominent in a wide array of industries.
Below are 8 key industries that significantly benefit from rapid injection molding, showcasing the diverse applications and use cases of this innovative technology.
- Automotive Industry: Utilizes rapid injection molding for parts such as interior panels, knobs, and connectors. This technology supports the industry’s need for durable, precision parts with quick turnaround times to keep pace with evolving design trends and regulatory requirements.
- Consumer Electronics: Employs rapid prototyping and tooling for the development of enclosures, buttons, and cases for smartphones, tablets, and other gadgets. Rapid injection molding enables the rapid iteration of designs, ensuring products meet consumer expectations for functionality and aesthetics.
- Medical Devices: Benefits from the high precision and repeatability of rapid injection molding for the production of components like syringe pumps, inhalers, and diagnostic devices. The ability to use medical-grade materials makes it a preferred choice for this sector.
- Aerospace: Leverages rapid injection molding for the creation of lightweight, high-strength parts such as interior cabin components and air ducts. The technology’s precision and material versatility meet the industry’s strict standards for safety and performance.
- Consumer Goods: Applies rapid injection molding to produce a wide range of products, from toys and household items to sports equipment. This process allows for the cost-effective customization and fast market introduction of new products.\
- Construction: Uses rapid injection molding for manufacturing components like fasteners, connectors, and fittings. The technology’s ability to produce durable, complex parts rapidly is highly valued in the construction sector.
- Agriculture: Benefits from rapid injection molding for parts such as irrigation system components and machinery casings. The technology supports the development of robust, UV-resistant parts essential for outdoor agricultural applications.
- Defense and Security: Employs rapid injection molding for the production of high-strength, durable parts required for equipment such as firearms, communication devices, and protective gear. The process’s quick turnaround times are critical for meeting urgent defense needs.
- Rapid Prototyping: Essential for the fast development and testing of product designs across all industries. It allows engineers and designers to quickly evaluate the form, fit, and function of components, accelerating the iteration process and significantly reducing the time to market.
- Rapid Tooling: Offers a cost-effective solution for producing molds for injection molding, especially beneficial for short production runs and prototyping. This application is crucial for industries that require molds quickly to test market reactions or to start production of parts without the delays associated with traditional tooling methods.
Getting Started with Rapid Injection Molding
Embracing rapid injection molding is a strategic decision that can significantly enhance your product development process.
Selecting the right partner is crucial for the success of your rapid injection molding project. Here are key factors to consider:
- Experience and Expertise: Look for a provider with a proven track record in your industry or with parts similar to what you intend to produce.
- Technology and Capabilities: Ensure the service provider has state-of-the-art technology and the capability to handle your project’s specific requirements, including materials, precision, and volumes.
- Communication and Collaboration: A provider that values open communication and collaboration can significantly influence the outcome. The ability to work closely with their team will help refine your design and avoid potential issues.
- Quality and Timeliness: Check for certifications and standards compliance that indicate a commitment to quality. Assess their history of meeting deadlines and their procedures for quality control.
- Cost: While not the only factor, understanding the cost structure is important. A good provider offers competitive pricing without compromising on quality or speed.
In a nutshell, you can get your injection molded plastic part within a short span of time to market. To get the best quality of Rapid Injection Molding Services, get in touch with XinYang for a free quote. We’ll gladly offer advice about your best options. Combining our expertise, engineering capabilities, and advanced technology we can offer rapid tooling solutions
Preparing Your Design for Rapid Injection Molding: Tips and Best Practices
To ensure your design is optimized for rapid injection molding, consider the following tips:
- Simplify Your Design: Minimize unnecessary complexities that could complicate the molding process and increase costs.
- Uniform Wall Thickness: As mentioned earlier, maintaining a wall thickness between 1.5 and 2.5 mm helps prevent defects and ensures uniform cooling.
- Incorporate Draft Angles: Adding a draft angle to your design makes part ejection easier, reducing the risk of damage.
- Consider Mold Accessibility: Design your part with mold creation and part removal in mind, avoiding undercuts or intricate geometries that require complex mold actions.
- Material Selection: Choose the appropriate material based on the part’s application, considering factors such as strength, flexibility, and thermal resistance.
Conclusion
Rapid injection molding represents a significant advancement in manufacturing, offering speed, flexibility, and high-quality production.
The future outlook for rapid injection molding in the manufacturing industry is promising. As technologies evolve and demand for faster, more efficient production continues to rise, rapid injection molding will remain a crucial tool for innovators and manufacturers alike.
FAQs
1. Is rapid injection molding suitable for manufacturing complex parts?
Yes, rapid injection molding can manufacture complex parts. Advanced mold design and manufacturing technologies, like 3D printing and EDM, allow for intricate features and precise tolerances, making it ideal for complex components.
2. Does rapid injection molding produce durable parts?
Absolutely. By utilizing high-quality materials and precise manufacturing processes, rapid injection molding produces parts that meet or exceed the durability and performance standards of traditional injection molding methods.
3. Is rapid injection molding expensive?
The cost-effectiveness of rapid injection molding depends on the project scope. For low to medium volume productions and prototyping, it’s often more cost-efficient than traditional methods due to lower tooling costs and faster turnaround times.
Although there is always a premium to pay for an exceptionally speedy turnaround, rapid injection molding is quite affordable as compared to the traditional process. The cost is of it inexpensive than might be expected owing to the automation procedure of this sort of mold making.