Table of Contents
CNC Machining Evolution: Transforming Precision Manufacturing
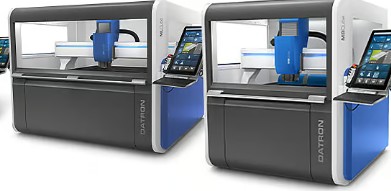
CNC machining is an important technology in modern manufacturing, revolutionizing the way intricate parts are fabricated in various industries with its precision feature. It has transformed production by providing unmatched accuracy, efficiency, and flexibility compared to traditional ways. This piece delves into the development, capabilities, and significance of CNC machining in today’s industrial sector.
Inception and Advancement
The history of CNC machining already been more than 80 years, And early forms of numerical control began to appear in the 1940s and 1950s, driven by the demand for more automated and repeatable manufacturing techniques, particularly in aerospace and defense industries. The incorporation of computers into machining started in the 1970s, marking a significant leap forward with the advent of CNC technology.
How CNC Machining Works
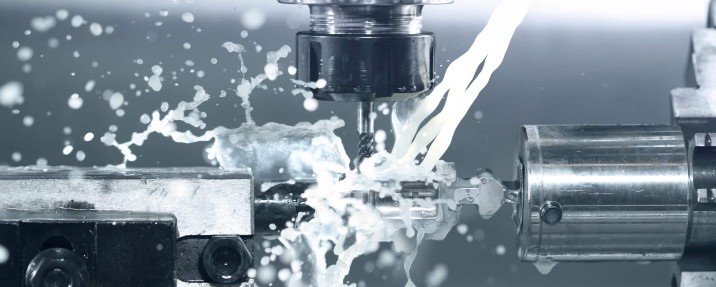
CNC machining is all about automating machine tool operations using programmed commands. These commands are stored in CAD files, detailing dimensions, tool paths, and cutting parameters. Advanced CNC systems rely on software to interpret these instructions and guide cutting tools with great accuracy, ensuring consistent part production and minimizing errors.
Application Areas For CNC Machining
Aerospace parts: Manufacturing aerospace parts for engine parts and high-precision fittings.
Automotive parts: Producing automotive parts including engines, braking parts, suspension parts, and other high-precision mechanical parts.
Electronics parts: Manufacturing circuit boards, switch housings, and various small precision parts.
Medical parts: Producing high-precision medical equipment and surgical tools, ensuring accuracy and reliability.
Advantages
Using CNC machining technology offers significant advantages:
. High Precision: Achieves machining accuracy down to microns, ensuring product dimension and quality stability.
. High Efficiency: High automation reduces human errors and time wastage, improving production efficiency.
. Flexibility: Quick adaptation to different machining requirements and design changes through program modifications.
. Cost-effectiveness: Despite higher equipment investment, long-term benefits include reduced labor costs and lower scrap rates.
Development Trends
In future, CNC machining technology will continue evolving in the following directions:
.Intelligence and Automation: More intelligent CNC systems capable of autonomous adjustment and process optimization.
.Multifunctionality: Integration of different machining functions to enhance equipment versatility and flexibility.
.Additive Manufacturing: Integration with technologies like 3D printing for complex structure fabrication and rapid prototyping.
.Green Manufacturing: Optimizing machining processes to reduce energy consumption and material waste, promoting environmental manufacturing practices.
conclusion
CNC machining technology, as an important technology in modern manufacturing, continues to evolve and enhance, injecting new vitality and possibilities into global manufacturing development. With advancements in technology and expanding application areas, CNC machining will insist to play a crucial role in improving product quality, enhancing market competitiveness, and driving industrial progress.